Repowered Oliver 1650 Looks Factory Fresh
 ✖  |
Andy Buelow’s 1650 Oliver looks original, but it’s not. It has a Cummins diesel under the hood as well as a 3-speed hydroshift from an 1855 Oliver. He repositioned the turbo and intake/exhaust hardware so they’re all hidden under the original tin. Even the exhaust exits through the original hole.
“The 1650 was the first tractor I ever drove,” says Buelow. “I always talked about repowering it with a diesel, and when the original gas engine started to fail, it was time.”
Buelow looked for a used diesel but couldn’t find one in his price range. The project got a jump-start when a good friend asked if he could leave his diesel pickup with Buelow. When asked how long it would be there, the friend replied, “Until you use the Cummins engine in your tractor. You’ve been talking about it as long as I’ve known you.”
Matching the diesel to the tractor’s drive was the next step. He could stick with the 1650 under/over hydroshift, but it had a 12-in. clutch. Buelow decided a larger clutch was needed to handle the extra power. Eventually, he located a 3-speed hydroshift and a 14-in. clutch in a salvaged 1855. After rebuilding it, he attached an SAE adapter plate that matched the engine.
A dry fit of engine and drive components identified alignment and clearance needs as well as fittings, including motor mounts. He cut away most of the old engine mounts, leaving part of the front mounts. This allowed him to fashion new mounts that would bolt to the Cummins, sit on the old casting, and bolt through to the frame.
Bolt holes at the rear of the motor match up with holes in the adapter plate, which matched up with holes in the 1855 bell housing.
“Once I had that figured out and had the alignment correct, I pulled the motor out and started to assemble the clutch,” says Buelow. “I realized the 1650 clutch linkage wouldn’t work in the 1855 bell housing. I built my own clutch lever so the original clutch pedal could be used.”
Throughout the process, an overriding rule of thumb was to keep the tractor looking stock. This began to complicate things if the exterior tin was to remain untouched. The turbo and intake/exhaust had to be relocated from hanging down from the rear of the engine, as there was no room.
To do that, he substituted a later model 24-valve manifold for the 12-valve manifold that came with the diesel. He flipped it upside down, which moved the turbo to the front of the engine and above it. However, the 24 had round exhaust ports, and the 12 had square, so Buelow had to machine holes on the manifold to taper from round out to square to make sure flow was unrestricted. He also had to machine a spacer to go between the turbo and the manifold to bypass fuel injector lines. He had to fabricate an oil supply line to the turbo and a drain tube from the bottom of the turbo.
The next step was dry-fitting the radiator and the hood. Buelow quickly realized the exhaust was shooting out the back of the turbo to the rear. The exhaust pipe hole in the hood was to the front of it.
“I bent the exhaust pipe in a U-shape to turn it back to the front so it makes a U over the top of the motor before making a 90-degree turn through the original hole,” says Buelow. “I also had to customize the intake plumbing from the turbo to the intake. It goes straight across the motor with a 45-degree turn into the intake.”
Buelow wanted to use the fan that came with the engine at the right distance from the tractor’s original radiator. This required a new hub and a spacer between the hub and the fan. He also needed new brackets to line the alternator up with the new hub. After laying out the fan hub bolt pattern on the motor, he drilled holes for it and threaded them. He drilled matching holes through the spacer and counter-bored them to leave a flat surface for the fan. He then drilled a second bolt pattern to attach the fan to the spacer. He shifted it a quarter turn from the first set of bolts and threaded them.
To this point in time, everything had been “dry fit.” Before final assembly, Buelow decided to split the tractor and check the transmission. After making support stands, he tore into the transmission, finding damaged splines on the input shaft and several damaged gears.
“I replaced them and put the tractor together for the first time,” says Buelow. “What a great feeling that was when it first fired up under the new power.”
While the tractor worked fine, it was still not back to “like new.” Buelow went through everything on it, sparing no expense. Finding an OEM canopy was key. The original canopy had been traded for a cab.
“I have a brother living in Georgia who found an Oliver in a salvage yard with a canopy,” says Buelow. “I was going to visit him anyway, so I took along my trailer.”
After adding some fuel, Buelow drove the tractor on the trailer and brought it home. Once there, he removed the canopy and resold the tractor for what he paid.
On a parts hunting trip to Minnesota, Buelow picked up parts that were in better shape than what was on the 1650. They included 3-pt. arms, a set of Oliver suitcase weights, and a set of fenders. One fender was in perfect shape; the other was almost perfect. He then saw a 1650 at a local auction with fenders, one of which was also in perfect shape.
“I bought it, drove it home, and swapped out the perfect fender for the nearly perfect fender,” says Buelow. “I switched out some other parts and resold it, making $1,500 on the deal. That helped offset much of the cost of the repower.”
One of the last items to be added to the Oliver was a loader. He found a loader only 15 miles away. In extremely good condition, all Buelow had to do was grind out some cracked welds and redo them. One change he made was to build an adapter plate so his skid steer implements could be used on the loader.
“I use the tractor every day,” says Buelow. “Everything works great, and we lost no functionality.”
Buelow’s father Dan told FARM SHOW that he had no doubt his son could do the job once he started. What amazes him is that he was able to do it with the tools he had available.
“We have a drill press I bought at auction years ago and a small metal lathe,” says Dan. “We have no CNC or other fancy tools. The tractor is awesome, and he basically did it all with hand tools in a single stall of a 2-stall garage.”
Buelow says the entire project took about 6 months of evenings and weekends. “I work road construction for 50 to 60 hrs. a week, coming home to work in the shop,” he says. “I called it a work in progress. My fiancé called it my mistress.”
Contact: FARM SHOW Followup, Andy Buelow, 17068 Middle Road, Dubuque, Iowa 52002 (ph 563-590-9287; Aj4wheelin@aol.com).
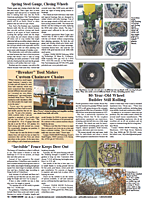
Click here to download page story appeared in.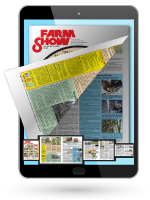
Click here to read entire issue
Repowered Oliver 1650 Looks Factory Fresh REPOWERED EQUIPMENT Andy Buelow’s 1650 Oliver looks original but it’s not It has a Cummins diesel under the hood as well as a 3-speed hydroshift from an 1855 Oliver and he repositioned the turbo and intake/exhaust hardware so that they’re all hidden under the original tin Even the exhaust exits through the original hole “The 1650 was the first tractor I ever drove ” says Buelow “I always talked about repowering it with a diesel and when the original gas engine started to fail it was time ” Buelow looked for a used diesel but couldn’t find one in his price range The project got a jump-start when a good friend asked if he could leave his diesel pickup with Buelow When asked how long it would be there the friend replied “Until you use the Cummins engine in your tractor You’ve been talking about it as long as I’ve known you ” Matching the diesel to the tractor’s drive was the next step He could stick with the 1650 under/over hydroshift but it had a 12-in clutch Buelow decided a larger clutch was needed to handle the extra power Eventually he located a 3-speed hydroshift and a 14-in clutch in a salvaged 1855 After rebuilding it he attached an SAE adapter plate that matched with the engine A dry fit of engine and drive components identified alignment and clearance needs as well as fittings including motor mounts He cut away most of the old engine mounts leaving part of the front mounts This allowed him to fashion new mounts that would bolt to the Cummins sit on the old casting and bolt through to the frame Bolt holes at the rear of the motor match up with holes in the adapter plate which matched up with holes in the 1855 bell housing “Once I had that figured out and had the alignment correct I pulled the motor out and started to assemble the clutch ” says Buelow “I realized the 1650 clutch linkage wouldn’t work in the 1855 bell housing I built my own clutch lever so the original clutch pedal could be used ” Throughout the process an overriding rule of thumb was to keep the tractor looking stock This began to complicate things if the exterior tin was to remain untouched The turbo and intake/exhaust had to be relocated from hanging down from the rear of the engine as there was no room To do that he substituted a later model 24-valve manifold for the 12-valve manifold that came with the diesel He flipped it upside down which moved the turbo to the front of the engine and above it However the 24 had round exhaust ports and the 12 has square so Buelow had to machine holes on the manifold to taper from round out to square to make sure flow was unrestricted He also had to machine a spacer to go between the turbo and the manifold in order to bypass fuel injector lines And he had to fabricate an oil supply line to the turbo and a drain tube from the bottom of the turbo The next step was dry fitting the radiator and the hood Buelow quickly realized the exhaust was shooting out the back of the turbo to the rear The exhaust pipe hole in the hood was to the front of it “I bent the exhaust pipe in a U-shape to turn it back to the front so it makes a U over the top of the motor before making a 90-degree turn through the original hole ” says Buelow “I also had to customize the intake plumbing from the turbo to the intake It goes straight across the motor with a 45-degree turn into the intake ” Buelow wanted to use the fan that came with the engine at the right distance from the tractor’s original radiator This required a new hub and a spacer between the hub and the fan He also needed new brackets to line the alternator up with the new hub After laying out the fan hub bolt pattern on the motor he drilled holes for it and threaded them He drilled matching holes through the spacer and counter bored them to leave a flat surface for the fan He then drilled a second bolt pattern to attach the fan to the spacer He shifted it a quarter turn from the first set of bolts and threaded them To this point in time everything had been “dry fit” Before final assembly Buelow decided to split the tractor and check the transmission After making support stands he tore into the transmission finding damaged splines on the input shaft and several damaged gears “I replaced them and put the tractor together for the first time ” says Buelow “What a great feeling that was when it first fired up under the new power ” While the tractor worked fine it was still not back to “like new ” Buelow went through everything on it sparing no expense Finding an OEM canopy was key The original canopy had been traded for a cab “I have a brother living in Georgia who found an Oliver in a salvage yard that had a canopy ” says Buelow “I was going to visit him anyway so I took along my trailer ” After adding some fuel Buelow was able to drive the tractor on the trailer and bring it home Once there he removed the canopy and resold the tractor for what he paid for it On a parts hunting trip to Minnesota Buelow picked up parts that were in better shape than what was on the 1650 They included 3-pt arms a set of Oliver suitcase weights and a set of fenders One fender was in perfect shape; the other was almost perfect He then saw a 1650 at a local auction with fenders one of which was also in perfect shape “I bought it drove it home and swapped out the perfect fender for the nearly perfect fender ” says Buelow “I switched out some other parts and resold it making $1 500 on the deal That helped offset much of the cost of the repower ” One of the last items to be added to the Oliver was a loader He found a loader only 15 miles away In extremely good condition all Buelow had to do was grind out some cracked welds and redo them One change he made was to build an adapter plate so his skid steer implements could be used on the loader “I use the tractor every day ” says Buelow “Everything works great and we lost no functionality ” Buelow’s father Dan told FARM SHOW that he had no doubt his son could do the job once he started What amazes him is that he was able to do it with the tools he had available “We have a drill press I bought at auction years ago and a small metal lathe ” says Dan “We have no CNC or other fancy tools The tractor is awesome and he basically did it all with hand tools in a single stall of a 2-stall garage ” Buelow says the entire project took about 6 months of evenings and weekends “I work road construction for 50 to 60 hrs a week coming home to work in the shop ” he says “I called it a work in progress My fiancé called it my mistress ” Contact: FARM SHOW Followup Andy Buelow 17068 Middle Road Dubuque Iowa 52002 ph 563 590-9287; Aj4wheelin@aol com